Top 10 Tips for Effective Pallet Storage Management in South Florida
Effective pallet storage management transforms warehouse operations from chaotic inventory handling into streamlined, cost-efficient systems that maximize space utilization and minimize handling costs. For South Florida businesses managing imports through Port of Miami and Port Everglades, proper pallet storage strategies directly impact profitability, safety, and customer satisfaction.
What Makes Pallet Storage Management Critical for Miami-Area Operations?
Pallet storage management encompasses the systematic organization, maintenance, and optimization of palletized inventory within warehouse facilities. Professional pallet storage goes beyond simply stacking goods—it involves strategic space planning, inventory rotation protocols, and safety procedures that protect both products and personnel while maximizing storage density.
South Florida's busy import trade creates unique pallet storage challenges. Container arrivals from Latin America and the Caribbean often contain floor-loaded cargo that requires professional palletization before storage. Miami Container Trucking's Fort Lauderdale facility processes thousands of containers annually, converting loose cargo into organized pallet storage systems that integrate seamlessly with modern distribution networks.
The region's climate adds complexity to pallet storage management, as humidity and temperature fluctuations can affect both wooden pallets and stored products. Professional facilities with climate-controlled zones and proper ventilation systems maintain product integrity while extending pallet lifespan, reducing replacement costs and protecting valuable inventory.
Top 10 Tips for Maximizing Pallet Storage Efficiency
1. Optimize Vertical Space with Strategic Racking Systems
Maximize warehouse capacity by implementing multi-level pallet racking systems that utilize available height while maintaining safe access for material handling equipment Choose racking configurations based on inventory turnover rates—selective racking for high-turnover items requiring frequent access, and drive-in systems for bulk storage of similar products.
Weight distribution plays a crucial role in vertical storage safety. Position heavier pallets on lower levels and lighter loads above to maintain stability and reduce tip-over risks MCT's 155,000 square foot warehouse utilizes optimized vertical storage systems with heavy-duty racking designed to safely handle loads up to 80,000 lbs while maximizing storage density.
2. Implement FIFO Inventory Rotation Systems
First-In, First-Out inventory management prevents product deterioration and reduces waste, particularly important for perishable goods and items with expiration dates. Establish clear rotation protocols that ensure older inventory moves before newer arrivals, maintaining product quality and minimizing loss due to aging.
Label pallet locations with receiving dates and product information to facilitate proper rotation. Digital tracking systems can automate FIFO compliance by generating pick lists that prioritize older inventory. Miami Container Trucking's warehouse management system provides real-time inventory tracking that supports efficient FIFO implementation for both short-term and long-term storage clients.
3. Maintain Proper Climate Control for Product Protection
Store pallets in dry, well-ventilated environments to prevent moisture damage, mold growth, and wooden pallet deterioration. Climate-controlled storage becomes essential for temperature-sensitive products including food items, pharmaceuticals, and electronics that can be damaged by South Florida's humidity and heat.
Monitor temperature and humidity levels continuously, particularly during summer months when mold risk increases8. Professional facilities implement automated climate monitoring systems that generate alerts when environmental thresholds are exceeded. MCT's warehouse includes dedicated climate-controlled zones specifically designed for products requiring environmental protection, with continuous monitoring systems that prevent temperature-related damage.
4. Establish Clear Labeling and Identification Systems
Implement comprehensive labeling systems that identify pallet contents, weight limits, handling instructions, and storage locations. Clear markings enable faster inventory retrieval, reduce handling errors, and improve overall warehouse efficiency by eliminating time spent searching for specific items.
Use standardized labeling formats that include SKU numbers, quantity counts, and destination information for outbound shipments. Barcode or RFID systems can automate inventory tracking and reduce manual data entry errors. Proper labeling becomes particularly important when managing mixed containers that require sorting and segregation during the palletization process.
5. Conduct Regular Pallet and Racking Inspections
Schedule routine inspections of both pallets and racking systems to identify damage before it creates safety hazards or inventory loss. Check for broken boards, protruding nails, bent racking components, and signs of overloading that could compromise structural integrity.
Replace or repair damaged pallets immediately rather than allowing them to remain in circulation where they can cause accidents or product damage. Professional warehouse operations maintain spare pallets and racking components to enable immediate repairs. Regular maintenance extends equipment lifespan and prevents costly emergency replacements that can disrupt warehouse operations.
6. Optimize Aisle Width for Equipment Efficiency
Balance storage density with equipment maneuverability by designing aisle widths that accommodate forklift operations while maximizing available storage space. Narrow aisles increase storage capacity but may reduce operational efficiency if equipment cannot move safely and quickly.
Consider the turning radius and operational requirements of material handling equipment when planning warehouse layout. Very narrow aisle (VNA) systems can maximize storage density in facilities with appropriate equipment and trained operators. MCT's warehouse layout optimizes aisle design for efficient cross-docking and material handling while maintaining safety standards for heavy cargo operations.
7. Implement Standardized Pallet Sizes and Types
Use uniform pallet dimensions to simplify storage planning, improve racking compatibility, and enable better space utilization predictions. Standard 48" x 40" pallets integrate seamlessly with most racking systems and transportation equipment, reducing handling complications and improving efficiency.
Select pallet materials appropriate for specific applications—wooden pallets for general cargo, plastic pallets for food products, and heavy-duty pallets for industrial equipment. Consider load capacity requirements and environmental conditions when choosing pallet types. Professional palletization services ensure appropriate pallet selection and construction for specific cargo requirements.
8. Establish Designated Storage Zones by Product Type
Organize warehouse space into zones based on product characteristics, turnover rates, and special handling requirements. High-turnover items should be positioned near loading docks, while bulk storage items can occupy deeper areas of the facility.
Create separate zones for different product categories such as hazardous materials, temperature-sensitive goods, and oversized items that require special handling procedures. This organization improves picking efficiency, reduces travel time, and ensures appropriate storage conditions for different product types. MCT's warehouse includes specialized areas for pallets, crates, and oversized cargo, with dedicated climate-controlled zones for sensitive products.
9. Train Personnel on Safe Handling Procedures
Provide comprehensive training on proper pallet handling techniques, including safe stacking methods, forklift operation, and warehouse safety protocols. Well-trained personnel reduce accident rates, prevent product damage, and improve overall operational efficiency.
Include training on proper lifting techniques for manual handling, emergency procedures, and equipment operation safety standards. Regular safety meetings and refresher training keep personnel current on best practices and regulatory requirements. Professional warehouse operations maintain detailed safety protocols and provide ongoing training to ensure safe handling of all cargo types.
10. Utilize Technology for Inventory Management
Implement warehouse management systems (WMS) that provide real-time inventory visibility, automated reorder alerts, and integration with customer systems. Technology reduces manual tracking errors, improves inventory accuracy, and enables data-driven optimization of storage operations.
Consider RFID tracking, barcode scanning, and automated inventory counting systems that streamline stock management processes. Advanced systems can predict storage needs, optimize picking routes, and generate performance analytics. MCT's warehouse management system integrates with customer platforms via API and EDI, providing real-time inventory data and supporting automated business processes.
How Climate and Location Impact Pallet Storage in South Florida
South Florida's subtropical climate creates specific challenges for pallet storage management that require specialized solutions. High humidity levels can cause wooden pallets to warp, develop mold, and deteriorate faster than in drier climates. Temperature fluctuations between air-conditioned warehouses and hot outdoor conditions can create condensation that affects both pallets and stored products.
Seasonal considerations become important for pallet storage planning. Summer months bring increased humidity and temperature that require enhanced ventilation and climate control. Hurricane season demands special preparations including securing tall pallet stacks and ensuring warehouse structural integrity can withstand severe weather conditions.
Proximity to major ports creates additional considerations for pallet storage management. MCT's strategic location 12 miles from Port Everglades and 30 miles from Port of Miami enables rapid container processing and pallet storage without extended transportation delays that can increase costs and complicate scheduling.
What Integration Options Support Efficient Pallet Storage Operations?
Modern pallet storage systems integrate with broader supply chain management platforms through warehouse management systems, EDI capabilities, and real-time tracking technologies. These integrations ensure pallet storage operations support overall business objectives while maintaining operational efficiency and customer service standards.
Cross-docking capabilities enable immediate transfer of palletized goods from inbound containers to outbound transportation without extended storage periods. This integration reduces inventory carrying costs while maintaining service levels for time-sensitive shipments. Professional facilities design operations to support just-in-time distribution strategies.
Technology integration connects pallet storage data to customer systems, providing visibility into stock levels and enabling automated reorder processes. Real-time inventory information supports demand planning, reduces stockouts, and improves customer satisfaction through accurate delivery commitments.
Key Takeaways for Implementing Effective Pallet Storage Management
Successful pallet storage management requires comprehensive planning that considers product characteristics, facility design, and operational workflows. Start by evaluating current storage processes to identify inefficiencies that professional management can address. Consider factors such as inventory turnover, product mix, and handling requirements when designing storage strategies.
Choose storage partners that offer integrated services including container handling, professional palletization, and distribution coordination. MCT's comprehensive approach handles container pickup from port terminals, expert palletization, secure storage, and coordinated delivery to final destinations. This integration reduces handoffs, improves coordination, and often provides cost savings compared to managing multiple service providers.
Focus on scalability when implementing pallet storage systems, as business growth and seasonal fluctuations can change storage requirements significantly. Flexible storage solutions allow adjustment of space and services without long-term commitments that may not match evolving business needs. Professional warehouse management systems provide the visibility and control needed to optimize storage utilization while supporting broader supply chain objectives.
For comprehensive pallet storage solutions in South Florida, explore our Pallet Storage Services or contact our team to discuss your specific warehousing and storage management requirements.
You May Also Like
These Related Stories
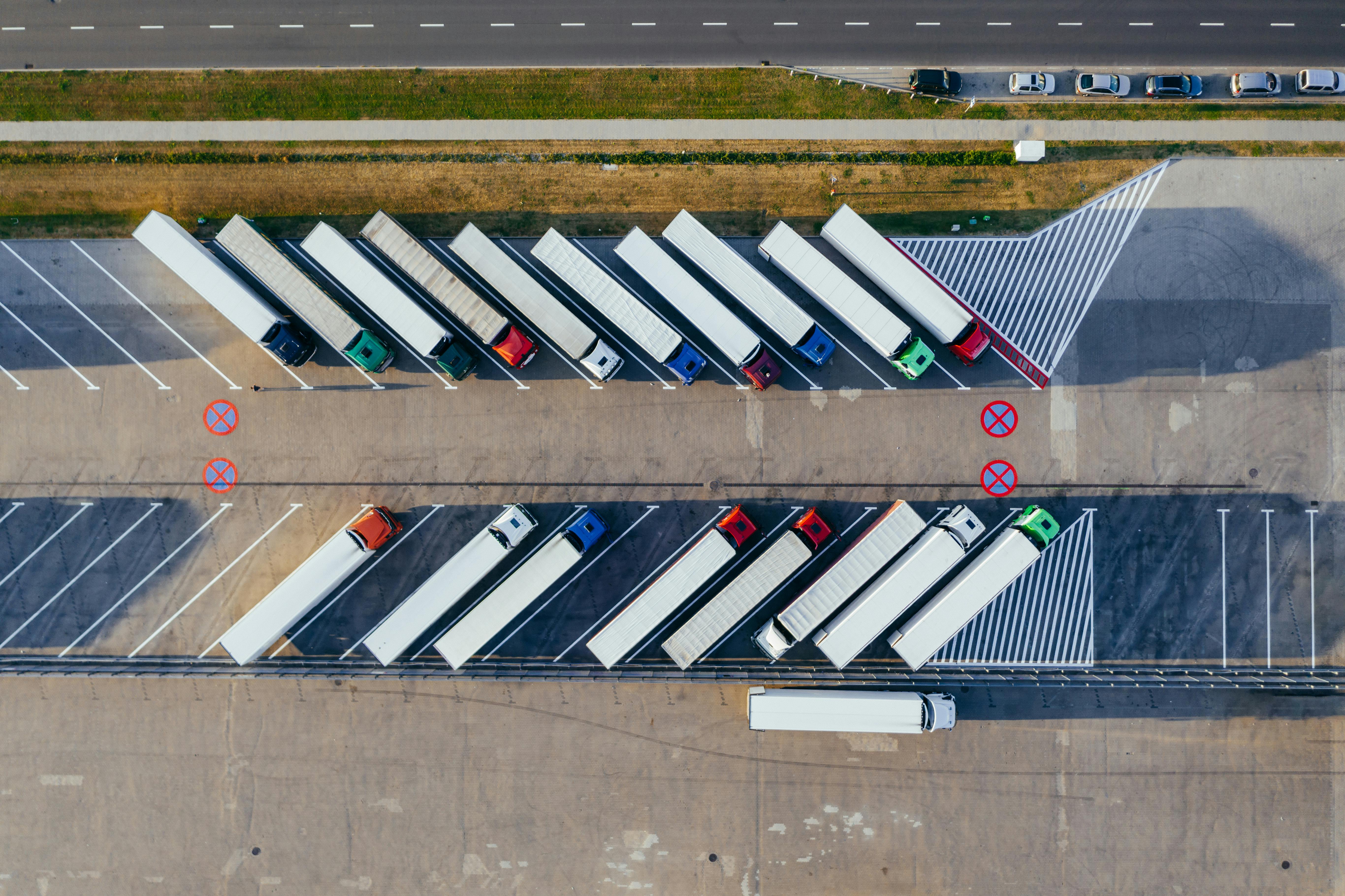
A Guide to Understanding Drayage & Calculating Drayage Costs in Logistics
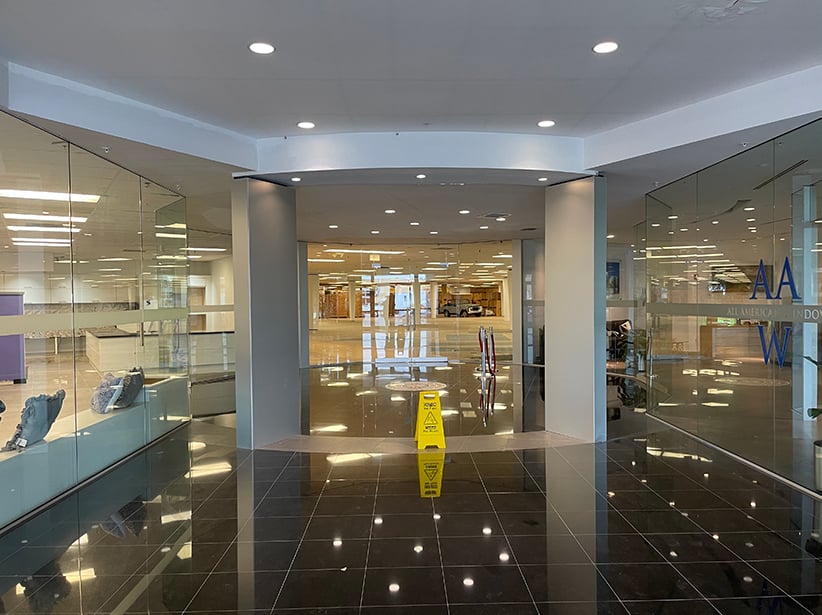
Best Miami Florida Warehouse Locations for Small Businesses
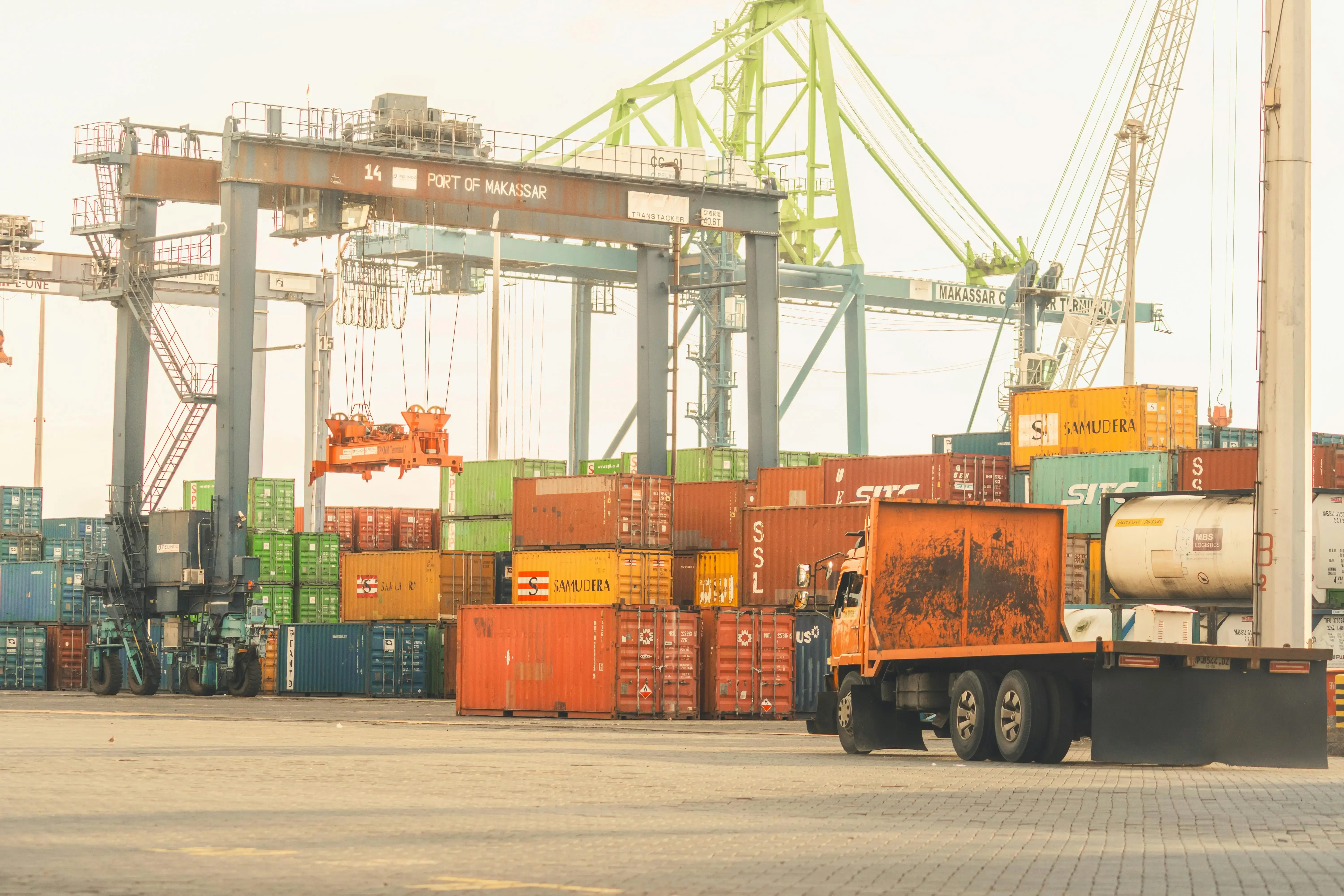