Cost Analysis: Pallet Storage Facilities vs. On-site Storage
Professional pallet storage facilities offer significant cost advantages over on-site storage for South Florida businesses managing imports through Port of Miami and Port Everglades. Comprehensive cost analysis reveals that third-party pallet storage reduces capital investment, operational expenses, and overhead costs while providing superior flexibility and scalability for growing businesses.
What Are the True Costs of On-site vs. Facility-Based Pallet Storage?
Cost analysis between pallet storage facilities and on-site storage extends far beyond simple rental rates, encompassing capital investments, operational expenses, and hidden costs that impact total ownership expenses. For Miami-area importers handling containers from Latin America and the Caribbean, understanding these comprehensive cost structures enables informed decisions that significantly impact profitability.
On-site pallet storage requires substantial upfront capital for warehouse space, racking systems, material handling equipment, and safety infrastructure. A basic warehouse setup capable of storing 500 pallets demands investments of $200,000 or more before considering ongoing operational costs. Professional pallet storage facilities eliminate these capital requirements while providing immediate access to sophisticated storage systems and experienced personnel.
Miami Container Trucking's Fort Lauderdale facility demonstrates the infrastructure advantages of professional pallet storage. The 155,000 square foot warehouse includes heavy-duty racking systems, climate-controlled zones, and 20 loading docks designed to handle loads up to 80,000 lbs. This level of infrastructure would require millions in capital investment for individual businesses to replicate independently.
How Do Monthly Costs Compare Between Facility and On-site Storage?
Professional pallet storage facilities like MCT offer competitive rates starting at $19 per month, providing predictable monthly expenses without capital investment or long-term real estate commitments. This rate includes secure storage, professional handling, and access to sophisticated warehouse management systems that would cost thousands to implement independently.
On-site storage costs include warehouse lease or purchase, racking installation, material handling equipment, insurance, utilities, and personnel expenses. In South Florida's expensive real estate market, warehouse space costs $8-12 per square foot annually, requiring 8-10 square feet per pallet position when including aisle space. This means on-site storage costs $6-10 per pallet monthly before considering equipment, labor, and operational expenses.
Hidden costs of on-site storage compound quickly: maintenance, security systems, HVAC for climate control, pest management, and compliance requirements. Professional facilities spread these costs across multiple clients, achieving economies of scale impossible for individual operations. MCT's warehouse includes 24/7 surveillance, gated access, and climate monitoring systems that would cost individual businesses tens of thousands annually to implement and maintain.
What Labor and Operational Cost Savings Do Facilities Provide?
Labor represents the largest operational cost difference between on-site and facility-based pallet storage. Professional warehouses employ trained personnel with specialized material handling certifications, spreading labor costs across multiple clients. Individual businesses must hire, train, and retain warehouse staff while maintaining coverage for sick days, vacations, and peak demand periods.
Operational efficiency improvements in professional facilities reduce handling costs through optimized workflows and specialized equipment. MCT's team processes thousands of containers annually, developing expertise in efficient palletization, inventory management, and order fulfillment that individual operations cannot match. This experience translates to faster processing times and reduced labor costs per pallet handled.
Technology investments in professional facilities provide cost savings through automated inventory tracking, reduced errors, and improved space utilization. Warehouse management systems eliminate manual tracking errors, reduce labor requirements, and optimize storage density. Individual businesses would need to invest tens of thousands in similar technology while lacking the volume to justify the expense.
How Do Capital Investment Requirements Compare?
Professional pallet storage eliminates capital investment requirements that can strain business cash flow and limit growth opportunities. Starting pallet storage services at $19 per month allows businesses to redirect capital investments toward core operations, inventory expansion, or market development rather than warehouse infrastructure.
On-site storage requires significant capital for warehouse space, racking systems, forklifts, and safety equipment. Basic warehouse setup costs include $50-80 per square foot for racking systems, $25,000-50,000 for forklifts, $10,000-20,000 for security systems, and ongoing maintenance expenses. These investments tie up capital that could generate higher returns in core business activities.
Equipment depreciation and replacement costs add ongoing capital requirements for on-site operations. Forklifts require replacement every 5-7 years, racking systems need periodic repairs and expansions, and technology systems require regular updates. Professional facilities spread these costs across multiple clients while maintaining state-of-the-art equipment that individual businesses cannot justify.
What Flexibility Advantages Reduce Long-term Costs?
Professional pallet storage provides scalability advantages that reduce long-term costs through flexible capacity adjustment. Businesses can increase or decrease storage requirements based on seasonal demand, market conditions, or growth trajectories without long-term lease commitments or infrastructure investments.
MCT's flexible storage agreements allow businesses to adjust space requirements monthly, accommodating seasonal inventory fluctuations or business growth without penalty. This flexibility prevents over-investment in warehouse capacity during slow periods while ensuring adequate space during peak seasons. On-site storage requires fixed capacity investments that may remain underutilized.
Location flexibility enables businesses to test new markets or adjust distribution strategies without relocating entire warehouse operations. Professional facilities provide strategic positioning near ports and transportation networks that individual businesses cannot achieve cost-effectively. MCT's location 12 miles from Port Everglades and 30 miles from Port of Miami provides optimal access to container imports without the real estate costs of port-adjacent locations.
How Do Risk Management and Insurance Costs Compare?
Professional pallet storage facilities provide comprehensive insurance coverage and risk management that reduces costs and liability exposure for businesses. MCT maintains insurance coverage protecting stored goods against theft, fire, natural disasters, and handling damage. Individual businesses must purchase separate coverage while accepting higher deductibles and risk exposure.
Security investment requirements for on-site storage include surveillance systems, access controls, alarm systems, and security personnel. Professional facilities spread these costs across multiple clients while maintaining higher security standards than individual businesses can afford. MCT's 24/7 surveillance, gated access, and professional security protocols provide protection levels exceeding most individual warehouse operations.
Compliance costs for safety regulations, environmental standards, and industry requirements are managed by professional facilities as part of their service offering. Individual businesses must invest in compliance expertise, training, and documentation while facing penalties for violations. Professional facilities maintain compliance expertise and bear responsibility for regulatory adherence.
What Technology and Efficiency Cost Benefits Exist?
Modern warehouse management systems in professional facilities provide technology advantages that reduce operational costs and improve efficiency. Real-time inventory tracking, automated reorder alerts, and integration capabilities eliminate manual processes that increase labor costs and error rates in individual operations.
MCT's warehouse management system integrates with customer platforms via API and EDI, providing real-time inventory data and supporting automated business processes. Individual businesses would need to invest $50,000-100,000 in similar technology while lacking the volume to justify advanced features. Professional facilities provide enterprise-level technology at shared costs.
Operational optimization through professional management reduces handling time, improves space utilization, and minimizes damage rates. Experienced warehouse teams implement best practices that individual businesses must develop through trial and error. This expertise translates to lower per-unit handling costs and improved inventory turnover rates.
How Do Transportation and Distribution Costs Compare?
Strategic location advantages of professional facilities reduce transportation costs through proximity to ports, highways, and distribution networks. MCT's Fort Lauderdale location provides immediate access to both major South Florida ports while connecting to I-95 and regional highway systems for efficient distribution.
Consolidation opportunities in professional facilities reduce transportation costs through shared trucking resources and optimized routing. Multiple businesses can share transportation costs for similar destinations while individual on-site operations must arrange separate transportation. This consolidation can reduce per-unit shipping costs by 20-30% compared to individual arrangements.
Cross-docking capabilities in professional facilities enable immediate transfer from inbound containers to outbound transportation without storage delays. This efficiency reduces inventory carrying costs while maintaining service levels for time-sensitive shipments. Individual facilities rarely have the volume or infrastructure to support efficient cross-docking operations.
What Climate Control and Specialized Storage Cost Implications Exist?
Climate-controlled storage requirements add significant costs to on-site operations through HVAC systems, monitoring equipment, and energy consumption. South Florida's climate demands continuous humidity and temperature control that can double utility costs for warehouse operations. Professional facilities spread these costs across multiple clients while maintaining optimal conditions.
Specialized storage requirements for different product types require dedicated areas and equipment that individual businesses cannot justify. MCT's warehouse includes dedicated climate-controlled zones, heavy-duty racking for industrial equipment, and specialized handling areas for oversized cargo. These capabilities would require significant additional investment for individual operations.
Environmental monitoring and maintenance costs for climate control systems require technical expertise and ongoing investment. Professional facilities employ specialized maintenance teams and monitoring systems that ensure optimal conditions while individual businesses must hire contractors or develop internal expertise at higher per-unit costs.
Key Financial Takeaways for Pallet Storage Decision-Making
Total cost of ownership analysis reveals that professional pallet storage provides significant cost advantages over on-site operations through reduced capital investment, lower operational expenses, and improved efficiency. The $19 per month starting rate at MCT includes services and infrastructure that would cost individual businesses significantly more to replicate.
Cash flow advantages of professional storage enable businesses to preserve capital for growth investments while accessing enterprise-level warehouse capabilities. Predictable monthly expenses simplify budgeting and financial planning compared to variable costs and unexpected capital requirements of on-site operations.
Scalability benefits allow businesses to optimize storage costs based on actual requirements rather than fixed capacity investments. This flexibility becomes particularly valuable during economic uncertainty or market expansion when storage needs may fluctuate significantly.
For businesses evaluating pallet storage options in South Florida, consider the comprehensive cost analysis beyond simple per-pallet rates. Professional facilities like Miami Container Trucking provide integrated solutions that reduce total supply chain costs while improving service levels and operational flexibility.
MCT's pallet storage services start at $19 per month and include access to our 155,000 square foot climate-controlled facility, professional handling, and integrated drayage services. Our comprehensive approach handles container pickup from port terminals, expert palletization, secure storage, and coordinated delivery to final destinations under one roof.
For comprehensive pallet storage solutions that reduce costs and improve efficiency, explore our Pallet Storage Services or contact our team to discuss your specific warehousing and cost optimization requirements.
You May Also Like
These Related Stories
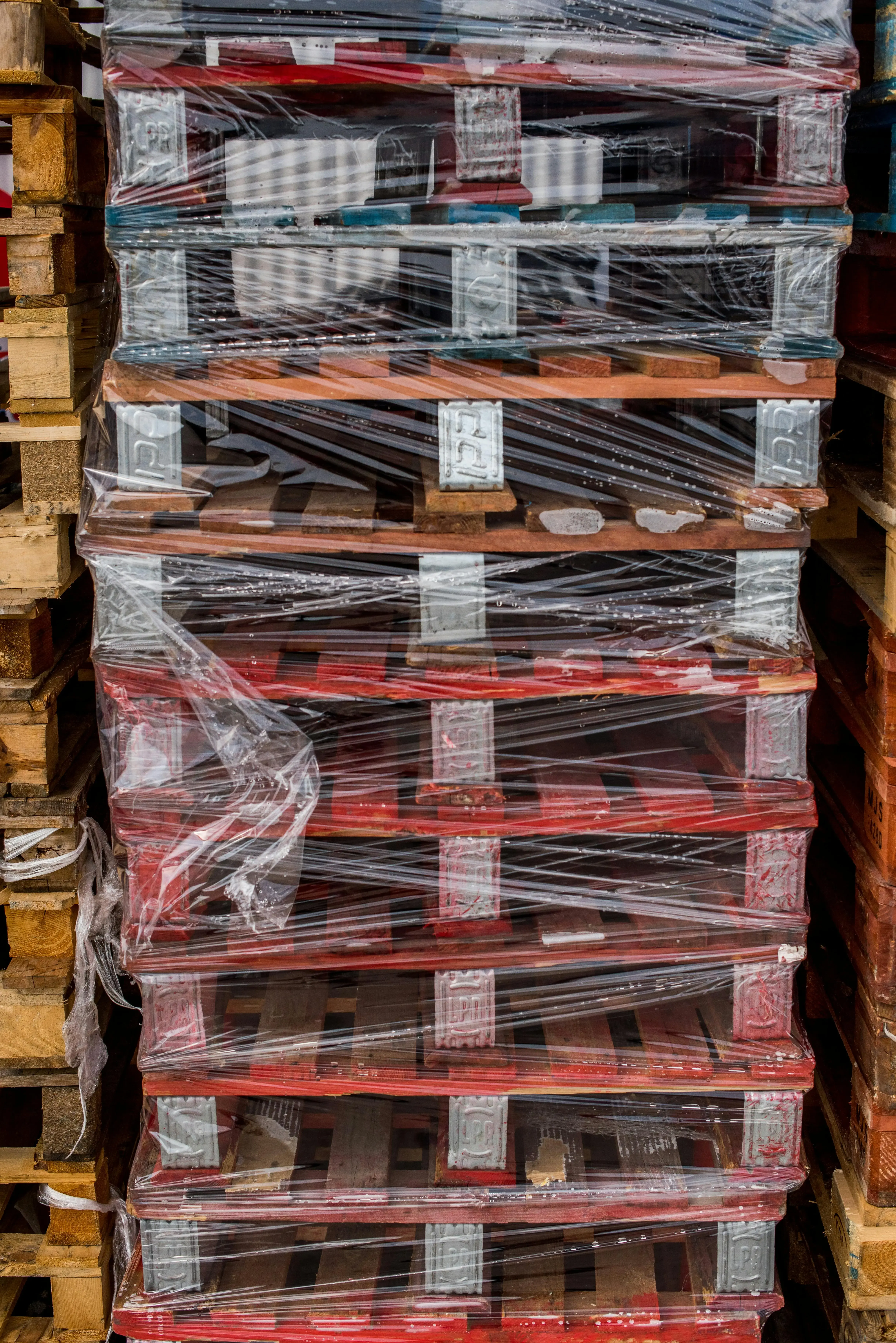
Seasonal Storage Challenges Solved by Pallet Storage in South Florida
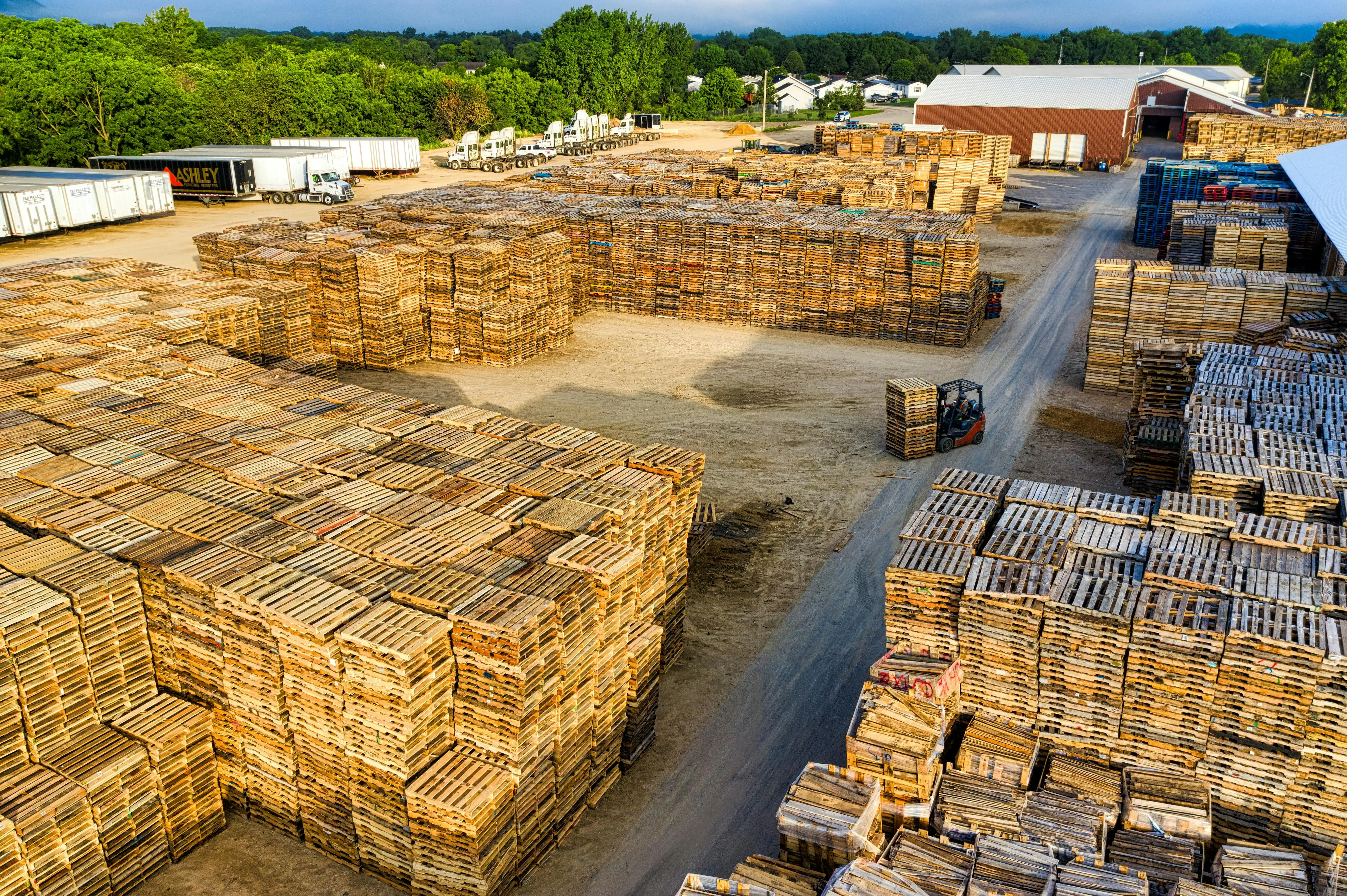
Understanding Pallet Storage Costs and Pricing Models in South Florida
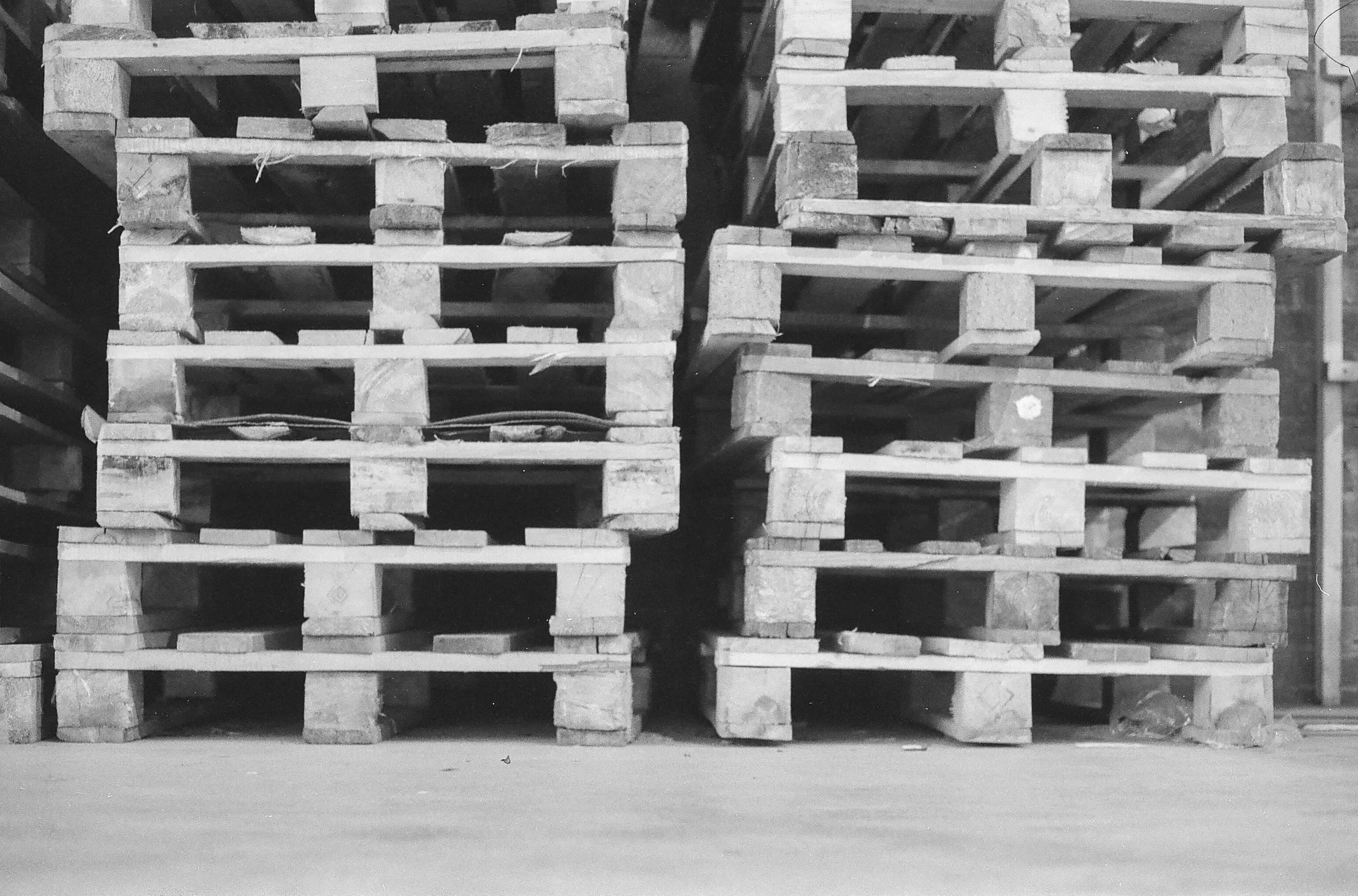